5 Ton Explosion-Proof Hook, Inspection, Quality & Safety
5-ton explosion-proof hook designed for hazardous areas, featuring complete inspection, third-party certification, and reliable load handling.
Explosion Proof Crane Kit -Explosion Proof Hook
When working in hazardous environments, safety is always the top priority. Explosion-proof hooks play a critical role in ensuring lifting operations are carried out safely in areas where flammable gases, dust, or vapors may be present. These hooks are specially designed to prevent any potential sparks or heat that could trigger an explosion.
Why Explosion-Proof Hooks Matter
Explosion-proof hooks are essential in industries like petrochemicals, mining, pharmaceuticals, and grain storage, where even the smallest spark can be catastrophic. In these environments, using the wrong equipment could lead to accidents, fires, or worse. That's why it's important to ensure that all lifting equipment, like hoists and cranes, includes explosion-proof components, particularly hooks.
What to Look for in a Reliable 5-Ton Explosion-Proof Hook
When selecting a 5-ton explosion-proof hook, a few things should be non-negotiable:
- Certification: Always check if the hook is certified for use in hazardous areas, such as meeting ATEX or IECEx standards. These certifications confirm that the hook has been tested to prevent sparks or overheating.
- Material: Make sure the hook is made from high-quality, non-sparking materials, like stainless steel (304), which is resistant to corrosion and wear.
- Load Capacity: The hook must be able to handle the weight of your loads—5 tons in this case—without compromising safety.
The Purpose of Inspection and Certification
The inspection and certification process for explosion-proof hooks is all about making sure the equipment is safe to use in these risky environments. A detailed inspection verifies:
- Material integrity and strength through various tests like tensile, impact, and hardness tests.
- Explosion-proof capabilities through non-destructive testing (NDT) like ultrasonic testing (UT).
- Compliance with international standards to ensure the hook will not fail under pressure.
By passing these rigorous checks, the hook becomes a reliable part of your safety system.
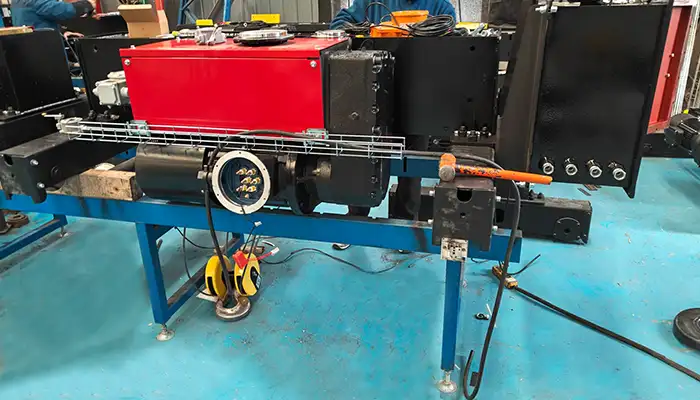
Product Overview
- Product Name: 5-Ton Explosion-Proof Hook - 5 ton explosion proof crane kit for sale pakistan project
- Product Number: HZ20241012083
- Material: Stainless Steel (304)
- Quantity: 10 pieces
- Furnace Batch No.: ZA24-682
- Heat Treatment: Normalizing
- Intended Use: The 5-ton explosion-proof hook is designed for safe lifting in explosive or hazardous environments. It's suitable for use in industries like oil refineries, chemical plants, and flour mills, where safety is a priority, and any spark or spark-inducing material could lead to accidents.
![5-Ton Explosion-Proof Hook - 5 ton explosion proof crane kit for sale pakistan project 5-Ton Explosion-Proof Hook - 5 ton explosion proof crane kit for sale pakistan project]()
Chemical Composition and Material Standards
The hook is made from high-quality 304 stainless steel, a durable and corrosion-resistant material, ideal for use in tough, hazardous environments.
Chemical Composition Breakdown:
- Carbon (C): 0.032%
- Manganese (Mn): 1.17%
- Silicon (Si): 0.56%
- Sulfur (S): 0.011%
- Phosphorus (P): 0.029%
- Chromium (Cr): 18.05%
- Nickel (Ni): 8.06%
These elements are crucial for enhancing the hook's overall strength, resistance to corrosion, and non-sparking properties. For example, Chromium (Cr) and Nickel (Ni) are key for ensuring the material's durability, especially in harsh and chemically active environments.
Standards and Compliance:
- The chemical composition aligns with industry standards GB/T 10051.1 and GB/T17107, which outline requirements for material quality, performance, and safety.
The careful selection of these elements ensures that the hook not only meets stringent safety requirements but also remains reliable under the pressures and demands of hazardous work environments. The 304 stainless steel material is corrosion-resistant, preventing breakdown or weakening over time due to exposure to chemicals, moisture, and extreme temperatures.
Non-Sparking Alloys and Corrosion Resistance
Using non-sparking alloys in explosion-proof hooks is a must in environments like oil refineries or chemical plants. Any spark or heat from the lifting equipment could ignite surrounding flammable substances, which is why the materials are carefully chosen to minimize that risk.
- Non-sparking alloys: These materials prevent accidental ignition. The selection of 304 stainless steel ensures that the hook doesn't generate sparks under stress.
- Corrosion resistance: The hook's ability to resist rust and chemical damage makes it an excellent choice for long-term use in corrosive or humid environments.
This combination of material properties and strict adherence to industry standards ensures that the 5-ton explosion-proof hook is a safe and reliable option for lifting in hazardous environments.
Mechanical Properties and Performance
The 5-Ton Explosion-Proof Hook is built for performance and durability in hazardous environments, where load-bearing capacity and resistance to extreme conditions are essential. The hook undergoes rigorous testing to meet the required standards for mechanical performance.
Test Items:
- Tensile Test: Measures the maximum amount of force the hook can withstand before breaking.
- Impact Test: Determines the hook's ability to resist sudden, high-force impacts.
- Hardness Test: Assesses the surface hardness to ensure the hook can endure heavy loads and rough environments.
Standard Properties:
The hook's mechanical properties are compared against established industry standards. The required standards are:
- Yield Point (Y.P.): ≥205 N/mm²
- Tensile Strength: ≥520 N/cmm²
- Elongation: ≥40%
- Surface Hardness: ≤187 HB
These properties ensure that the hook can handle the heavy lifting demands typically found in hazardous industrial environments. The test results for the hook exceed or meet these standards, confirming that it is suitable for safe operation in tough conditions.
Test Results:
Sample test results showed the following performance:
- Yield Point (Y.P.): 239 N/mm²
- Tensile Strength: 604 N/cmm²
- Elongation: 64%
- Surface Hardness: 161 HB
These results confirm that the hook has superior mechanical properties, ensuring reliable and safe performance under the required load and stress. The elongation percentage and tensile strength demonstrate that the hook can stretch and absorb energy before failure, which is crucial in lifting operations.
Performance Expectations:
The 5-ton explosion-proof hook is designed to:
- Handle high loads without failure, supporting up to 5 tons safely.
- Withstand extreme conditions such as chemical exposure, high humidity, and fluctuating temperatures.
- Last longer due to its high resistance to wear, corrosion, and impact.
These performance qualities make it ideal for use in environments like chemical plants, oil refineries, and flour mills.
Non-Destructive Testing (NDT) and Methods
To ensure the hook's material integrity and explosion-proof performance, non-destructive testing (NDT) is conducted using advanced ultrasonic testing equipment.
Testing Equipment:
- PXUT-330 Ultrasonic Testing (UT): This equipment is used to detect internal flaws or inconsistencies in the hook material without damaging it.
- Coupling Agent: Oil is used as a coupling agent to improve the ultrasonic testing results by enhancing sound wave transmission between the probe and the hook.
Testing Methodology:
- Longitudinal Wave Testing: Used to detect flaws along the length of the hook, providing information on internal cracks or voids.
- Transverse Wave Testing: Helps identify any surface or internal imperfections that could compromise the hook's strength and safety.
Surface Condition:
- The hook is polished smooth to ensure that there are no surface defects that could interfere with the ultrasonic testing. This smooth surface also helps to minimize the risk of sparks or other dangers caused by rough edges or material inconsistencies.
Calibration:
- Sensitivity Levels: The ultrasonic equipment is calibrated to specific sensitivity levels to ensure precise and accurate test results.
- Calibration Method: The test equipment is regularly calibrated according to industry standards to guarantee the reliability of the test results and compliance with explosion-proof requirements.
By using these advanced non-destructive testing methods, the manufacturer can verify the integrity of the 5-ton explosion-proof hook, ensuring it meets safety standards and is suitable for use in hazardous environments.
Certification and Compliance
The 5-Ton Explosion-Proof Hook is not only built for performance but also undergoes a rigorous certification process to ensure it meets the highest safety standards for use in hazardous environments. Compliance with recognized standards guarantees the hook's reliability and safety.
Standards Applied:
The hook adheres to the GB10051-2010 standard, which outlines the technical requirements for explosion-proof equipment used in industrial environments. Compliance with this standard ensures the hook is tested for both durability and safety, meeting specific criteria for materials, design, and performance under harsh conditions.
- Explosion-proof Requirements: The hook's design incorporates safety features that prevent sparks and ignition in explosive atmospheres. It's specifically built to reduce the risk of accidents in hazardous environments such as oil refineries, chemical plants, and grain mills.
Certified Testing:
Certified testing ensures that the 5-ton explosion-proof hook undergoes thorough inspections to meet all required explosion-proof specifications. These tests cover mechanical performance, material integrity, and resistance to environmental factors like corrosion and impact. The hook is tested for:
- Explosion-proof capability: Ensuring it won't cause ignition or sparks that could trigger an explosion in volatile areas.
- Material strength: Confirming the hook's ability to support heavy loads without failure.
- Surface integrity: Ensuring that the hook's surfaces are smooth and free from defects that could lead to mechanical failure.
Only after passing these strict tests does the hook receive its certification, guaranteeing it is safe and reliable for use in explosive or hazardous environments.
![5-Ton Explosion-Proof Hook - 5 ton explosion proof crane kit for sale pakistan project 5-Ton Explosion-Proof Hook - 5 ton explosion proof crane kit for sale pakistan project]()
Certification Levels:
Explosion-proof hooks are certified based on their suitability for different hazardous zones, which are classified according to the type and likelihood of an explosive atmosphere:
- Zones 1 & 2 (Gas): The hook is certified for use in areas where explosive gas mixtures are likely to occur (Zone 1) or occasionally present (Zone 2). This means it can safely operate in environments where gas or vapor hazards are a concern.
- Zones 21 & 22 (Dust): The hook is also certified for use in areas with combustible dust, where dust could form a potentially explosive atmosphere (Zones 21 and 22). These certifications ensure that the hook can be safely used in environments like flour mills and chemical plants, where dust hazards are prevalent.
How Certification Guarantees Safety:
Certification ensures that the 5-Ton Explosion-Proof Hook meets stringent safety requirements. In explosive environments, the smallest spark or malfunction can lead to catastrophic consequences. The certification process:
- Ensures reliable performance under hazardous conditions.
- Prevents ignition by making sure the hook's materials, coatings, and design reduce the risk of sparks.
- Protects workers by providing equipment that meets the necessary standards to keep operations safe and secure.
With certification, businesses can trust that their lifting operations in hazardous areas are not only efficient but also safe for their workers and the environment.
Inspection Process and Quality Control
Ensuring the quality and safety of the 5-Ton Explosion-Proof Hook involves a detailed and rigorous inspection process, which begins right from the initial manufacturing phase and continues through to final certification. The goal is to confirm the hook's ability to withstand hazardous environments while maintaining top-tier performance.
Inspection Process:
The inspection process follows a clear and systematic flow:
- Initial Testing: After the hook is manufactured, it undergoes preliminary mechanical tests to check its material properties, tensile strength, impact resistance, and hardness. This ensures that the hook is made of durable, high-quality material that meets the specified standards.
- Non-Destructive Testing (NDT): The hook is subjected to ultrasonic testing (UT), using specialized equipment like the PXUT-330. This checks the integrity of the material without damaging the hook. The test ensures there are no internal cracks, voids, or other issues that could jeopardize the hook's explosion-proof capability.
- Final Certification: After passing all preliminary tests, the hook undergoes a final round of rigorous inspections, including surface testing, calibration, and compliance checks. Only after meeting all requirements, it receives its certification for use in hazardous areas, particularly in explosive atmospheres.
Role of the Quality Control Department Supervisor and Inspector:
The Quality Control Department Supervisor and Inspector play crucial roles in ensuring that the hook meets all safety and performance standards.
- Quality Control Department Supervisor: Oversees the entire inspection process to ensure that each hook complies with industry standards and regulations. The supervisor ensures that every step of the testing process is executed accurately and consistently. They are responsible for confirming the reliability of the hook before it leaves the factory.
- Inspector: The inspector carries out detailed physical and non-destructive tests, verifying the mechanical properties, material quality, and safety features of the hook. They are responsible for documenting test results and ensuring that every hook passes the required inspection stages.
By maintaining stringent quality control, these experts guarantee that every 5-ton explosion-proof hook is safe, reliable, and ready for use in hazardous environments.
Ensuring Adherence to Stringent Safety Standards:
The primary goal of the inspection process is to ensure that the 5-ton explosion-proof hook adheres to safety standards set by international certifications such as ATEX and IECEx. Through continuous testing and verification, we ensure that:
- The hook is resistant to sparks and other ignition risks.
- It is made from corrosion-resistant, non-sparking materials.
- It meets the required load-bearing capacities and mechanical strength to safely operate in explosive atmospheres.
This meticulous attention to detail allows for maximum protection for workers and operational safety in industries where explosion-proof equipment is a necessity.
Applications and Industry Use Cases
The 5-Ton Explosion-Proof Hook is designed for industries where explosive gases, vapors, or dust are present, requiring lifting equipment that is safe, reliable, and certified to prevent sparks or ignition. These industries rely on the explosion-proof hook to ensure worker safety and operational efficiency.
Industries That Commonly Use 5-Ton Explosion-Proof Hooks:
- Petrochemical Industry: Explosion-proof hooks are crucial in areas where volatile gases like methane, hydrogen, or propane are commonly found. They ensure safe lifting of heavy loads in oil refineries and gas facilities without the risk of sparking.
- Mining Industry: In underground mining or coal production, dust and gas are ever-present hazards. Explosion-proof hooks help lift mining equipment and materials without causing sparks that could trigger explosions in such environments.
- Pharmaceutical Industry: Chemical plants and pharmaceutical manufacturing often use flammable substances. Explosion-proof hooks ensure safe lifting of chemicals and raw materials, reducing the risk of ignition.
- Paint Shops and Coating Facilities: Paints and coatings often contain volatile solvents that create explosive vapors. Explosion-proof hooks are essential for lifting large containers or materials in these environments safely.
- Flour Mills and Grain Storage: Dust from flour and grains can create explosive environments. Explosion-proof hooks help move heavy loads in these facilities without posing a spark risk, ensuring safety during everyday operations.
Specific Use Cases:
- Oil Refineries: Handling large containers of volatile chemicals or refining equipment requires explosion-proof lifting hooks to prevent ignition. In such an environment, any spark could lead to catastrophic consequences, making explosion-proof hooks essential for everyday operations.
- Chemical Storage and Handling: In chemical plants, lifting hooks must be able to withstand exposure to harsh chemicals without corroding or sparking. The 5-ton explosion-proof hook is ideal for lifting heavy, hazardous chemical containers in a safe and efficient manner.
- Flour Mills: The dust in flour mills can create an explosive atmosphere, making explosion-proof hooks necessary for handling large amounts of grain or flour. These hooks ensure that there is no risk of igniting dust particles during lifting operations.
In all of these applications, the 5-Ton Explosion-Proof Hook ensures safe lifting while protecting workers, equipment, and the environment from the dangers of ignition in explosive environments. Whether it's oil, chemicals, or dust, the hook provides reliable, certified safety that's crucial in industries handling dangerous materials.
Conclusion
The 5-Ton Explosion-Proof Hook has undergone a thorough and rigorous inspection and certification process to ensure its reliability and safety. From the initial mechanical tests to non-destructive testing and final certification, every step is carried out with precision to meet the highest standards in hazardous environments.
This explosion-proof hook has been certified to meet GB10051-2010 and other international standards like ATEX and IECEx, ensuring it can safely operate in explosive zones, including gas and dust environments. The use of non-sparking alloys, corrosion-resistant materials, and meticulous quality control guarantees the hook's durability, load-bearing capacity, and safety.
Whether used in petrochemical plants, mining operations, pharmaceutical facilities, or grain storage, the 5-ton explosion-proof hook provides the necessary protection for workers and equipment in high-risk environments.
For more information, technical consultation, or to get a personalized quote, feel free to contact us to get your cusomized explosion proof material handing equipment and components.
Article by Bella ,who has been in the hoist and crane field since 2016. Bella provides overhead crane & gantry crane consultation services for clients who need a customized overhead travelling crane solution.Contact her to get free consultation.